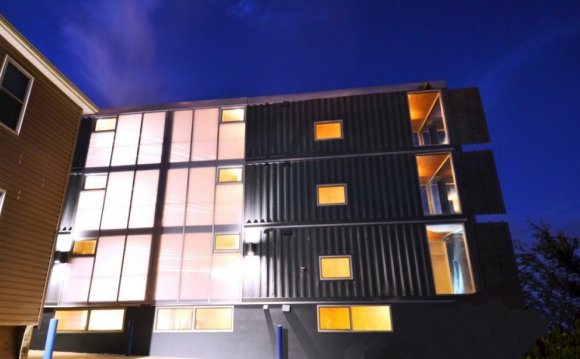
The exterior of a shipping-container building near Catholic University. (Greg Powers/For The Washington Post)
The interior of one of the bedrooms in the building, which is used for student housing. (Greg Powers/For The Washington Post)
A few weeks after the meeting at Miner Elementary, Price holed up inside Catholic’s architecture building, where he has taught since 1991, to critique student designs for a proposed container industrial park in Swinford, Ireland. The students used the containers like giant Lego bricks, stacking them to form larger boxy shapes or scattering them at odd angles.
Containers offer builders cost savings, time savings and flexibility. After delivering the sandblasted, repainted and cut units, which cost $1, 100 to $3, 500 each, prepping the site, stacking them and filling out the interior, the final construction tally comes in around $160 per square foot, Price said, compared with $225 per square foot for a conventional structure. (The cost savings comes mainly from not having to spend as much money on a building’s exterior structure .) Because 40 to 50 percent of the walls can be removed without harming the structural integrity, designers can add windows or combine containers to create larger interior spaces and aren’t limited to the containers’ dimensions of 8 feet wide by 9 feet 6 inches high by 40 feet long. And a building made out of used containers can be put up in half the time of a conventional one.
Price can rattle off these facts and figures, something his students are not as adept at yet. “You’re underselling it, ” he tells one mumbler. He wants his students to be skilled at pitching ideas in the real world of developers, zoning boards and skeptical neighbors. That comes easy to Price, who is a talker. When he gets going, he can be both punchy — “that flagstone ... is so patio suburban” — and ponderous — “nostalgically watered-down exterior decorating will shape our very human character into one monochromatic, bland whisper.”
Price was introduced to shipping containers in New Mexico during the 1970s when they were used in passive solar housing. Their moment passed with the energy crisis. He moved to Takoma Park, Md., in 1980 and built a practice in preservation and designing modernist buildings with minimalist interiors and lots of glass. Among them is his own 2004 house in the Forest Hills area of Northwest Washington with a copper-clad front, a glass bridge and a four-story wall of windows in the back.
The popularity of industrial-style and sustainable design led to a resurgence of “cargo chic” in the early aughts. By then global economic forces had created a chronic surplus of empty containers. According to Marc Levinson, an economist and author of “The Box, ” standardizing the size of the containers dramatically reduced the expense to ship goods from low-cost labor centers in Asia to markets in the West. Today, thanks to the West’s huge trade deficit with China, it can be more cost-effective to send new containers full of goods than to pay for used ones to be sent back empty. At any given time, experts estimate, 2.5 million containers are sitting empty around the world. That includes hundreds of thousands at U.S. ports such as Baltimore, which handled about 126, 000 empty containers in 2014, Maryland Port Administration spokesman Richard Scher said. Finding uses for the containers has become irresistible to eco-minded architects and consumers.
RELATED VIDEO
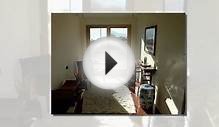
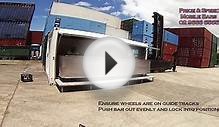
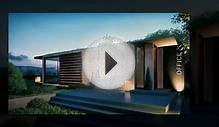